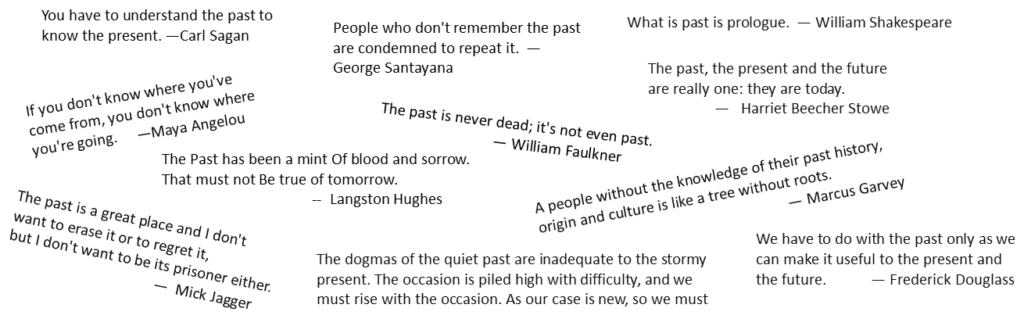
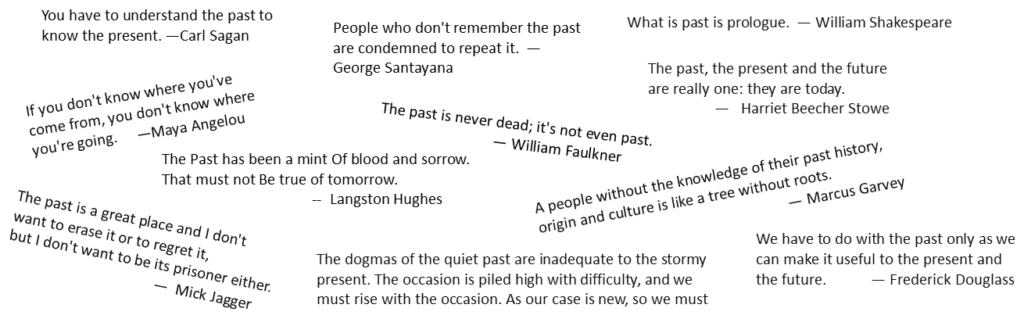
Treasure the past. Inspire the future.
Our project is a newly established fund that aims to use its limited resources to support preservation and archiving by smaller movement efforts and organizations.
The Archive Project aims to use the limited funds at its disposal to support work that advances its mission. That mission is to “preserve the records and other materials of groups and individuals who have made special contributions to social justice and transformation.” We aim to “promote scholarship and education about that history to impact understanding of contemporary issues and social movements and [to] develop educational materials and programs to that end.”